Exploring Polaris 50 Plastics: Manufacturing and Impact
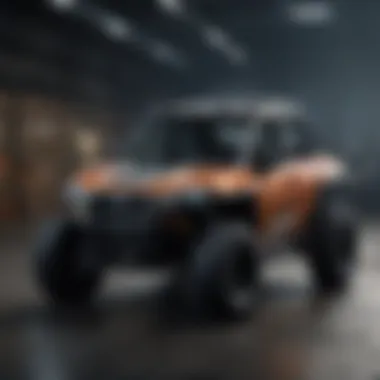
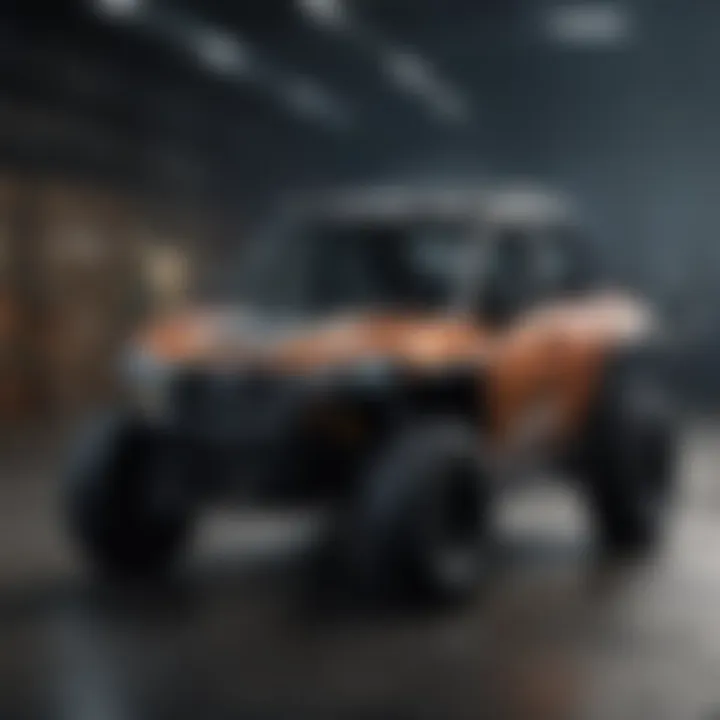
Intro
In the ever-evolving automotive and boating sectors, the role of materials cannot be overstated. Among these materials, plastic holds a significant position, particularly in the context of Polaris 50 models. As these vehicles continue to gain popularity, it becomes essential to scrutinize the types of plastics utilized in their construction, the implications of their properties, and the trends shaping their future.
Plastic has become a staple in modern automotive design, favored for its lightweight nature, resistance to corrosion, and cost-effectiveness. But it isn't just about keeping finances in check. There’s a whole world of innovation and sustainability tied to how these materials are crafted and employed in vehicles. This article takes a closer look at these dynamics, aiming to weave together the intricate details surrounding Polaris 50 plastics—how they're made, their performance metrics, and where they fit into larger environmental conversations.
From production to application, understanding these elements can enlighten automotive enthusiasts and industry professionals alike. So, let’s buckle up and dive into the current trends that highlight the role of plastics in the Polaris 50 lineup.
Prelims to Polaris Plastics
When we talk about Polaris 50 plastics, we dive into a world that plays a crucial role in the automotive industry, particularly for those enthusiasts who appreciate the intricacies of material science and design. These plastics not only provide functionality but also contribute significantly to the performance and aesthetics of vehicles. Understanding the significance of these materials is essential for those involved in automotive engineering, design, or even everyday use.
Definition and Relevance
Polaris 50 plastics refer to a range of synthetic materials specifically used in the production of components for Polaris 50 vehicles. These include various types of plastics designed to meet the demanding requirements of the automotive sector. The relevance of these plastics lies in their ability to offer lightweight durability, resistance to certain environmental factors, and versatility in applications ranging from exterior panels to interior fittings. As consumer preferences steadily shift towards more eco-friendly and efficient vehicle designs, the importance of understanding these materials becomes even more pressing. Automakers are always on the lookout for advancements that enhance performance without compromising on sustainability.
Historical Context
The use of plastics in the automotive field is not a novel concept; it has evolved over decades. Back in the mid-20th century, manufacturers like Polaris began exploring these materials to strategically improve vehicle designs. Initially, plastics were integrated to replace heavier metals, with an eye on weight reduction and improved fuel efficiency. Through the years, innovations in plastic manufacturing and formulation have led to the development of specialized plastics that cater uniquely to the needs of vehicles like the Polaris 50. This historical backdrop lays the foundation for understanding current trends and future directions in automotive plastic utilization. As we push forward, it’s essential to appreciate how far we’ve come and acknowledge the journey that has brought us to today’s advanced composite plastics.
Types of Plastics Used in Polaris
Understanding the varieties of plastics employed in the production of Polaris 50 components is crucial. This section sheds light on the specific characteristics, advantages, and notable applications of each type, illustrating their significance in the automotive sector. It reveals how the selection of materials impacts not just the functionality but also the longevity and environmental footprint of the vehicles. Each plastic type features unique qualities that contribute to overall performance, durability, and aesthetics, making them essential components in the Polaris 50 lineup.
Polypropylene
Polypropylene is a lightweight, versatile plastic with high resistance to impacts and chemicals. It is widely used in various automotive applications due to its excellent fatigue resistance, which is particularly beneficial in components that undergo repetitive stress. For example, parts like clips and fasteners can withstand significant strain without failing, maintaining their integrity over time.
Moreover, polypropylene’s low density contributes to overall vehicle weight reduction, enhancing fuel efficiency. Due to its insulating properties, it also aids in minimizing noise levels from the road and engine, providing a smoother ride. Some users often appreciate how it can be colored easily, allowing for customization in vehicle interiors and other visible components.
Polyethylene
Polyethylene is another staple in the world of automotive plastics, known for its toughness and flexibility. Its resilience against moisture and chemical exposure makes it ideal for applications such as fuel tanks and underbody components. The flexibility of polyethylene allows it to be molded into various shapes, accommodating different design requirements while ensuring durability.
This material also offers a degree of protection against impacts, which is crucial for parts that may face harsh conditions. Furthermore, its relatively low cost makes it an appealing choice for manufacturers looking to balance performance with budgetary constraints. By integrating polyethylene into their design, Polaris 50 vehicles benefit from a material that extends the lifespan of essential components.
Acrylonitrile Butadiene Styrene (ABS)
ABS stands out due to its strength and exceptional impact resistance. This thermoplastic is particularly valued in the automotive industry for applications that demand a high level of durability and aesthetic appeal. For instance, the material is often used for interior surfaces and trim components that require a premium finish while ensuring robustness against everyday wear and tear.
The ease of molding ABS into complex shapes further enhances its usability in vehicle design, allowing manufacturers to deliver more innovative features without compromising on strength. Its resistance to environmental stressors means parts made from ABS can maintain their aesthetic and functional qualities over the years, making it a go-to choice for many vehicle parts.
Polycarbonate
Polycarbonate is renowned for its transparency and high impact strength. In the Polaris 50, polycarbonate is predominantly utilized in light covers, windows, and other applications requiring clarity along with resilience. It can absorb significant impacts without shattering, which is essential for safety features and longevity in automotive parts.
Another important aspect of polycarbonate is its ability to withstand temperature fluctuations, making it highly suitable for environments that may experience extreme conditions. It is also relatively lightweight, enhancing overall vehicle efficiency, and its excellent UV resistance helps in reducing yellowness, thus maintaining visual quality over time.
In summary, each type of plastic used in the Polaris 50 plays a crucial role in enhancing performance, safety, and aesthetics. The integration of these materials not only reflects advancements in automotive engineering but also indicates a deeper understanding of consumer needs and environmental considerations. The ongoing evolution in plastic technologies promises even more innovative and sustainable solutions for the future.
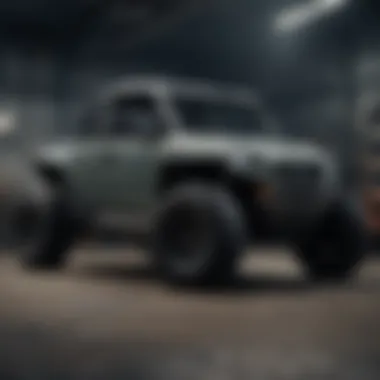
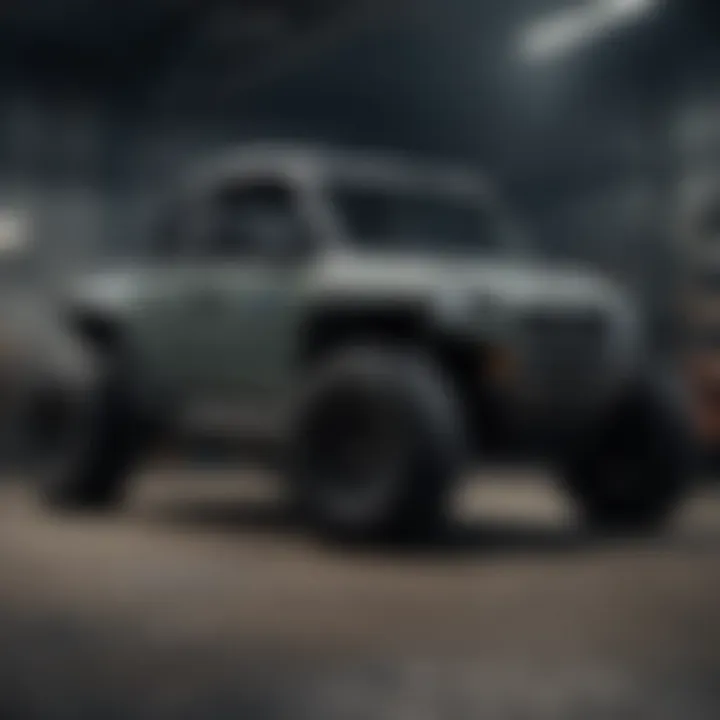
Manufacturing Processes of Polaris Plastics
The manufacturing processes associated with Polaris 50 plastics are fundamental to understanding how these materials come to be used in automotive applications. This section dives into the various methods employed in crafting these plastics, each possessing its own unique attributes that lend themselves to specific functional requirements. The efficiency, cost, and environmental impact of these processes are all vital considerations that shape the final product.
Injection Molding
Injection molding stands out as one of the principal methods used to produce Polaris 50 components. This technique involves injecting molten plastic into a mold, allowing it to cool and solidify into the desired shape. The capability for high-volume production is one of its key benefits.
- Precision: Injection molding achieves tight tolerances, making it ideal for parts that require exact specifications.
- Material Efficiency: This process minimizes waste, as the material that does not fill the cavity can often be reused.
- Complex Geometries: It allows for the production of intricate designs that would be difficult or impossible to achieve with other methods.
However, it’s not just a silver lining—there are factors to consider. The initial costs can be quite high due to mold fabrication. In addition, if the design of a component changes, fresh molds may be necessary. Thus, while injection molding is efficient for large volumes, its inflexibility can be a double-edged sword when dealing with rapid design changes.
Extrusion
Extrusion is another manufacturing process that deserves its moment in the spotlight. In this method, plastic granules are fed into a heated barrel, melted, and then forced through a die to create continuous shapes like sheets or tubes. For Polaris 50 plastics, extrusion is particularly useful in producing components like profiles and piping.
- Continuous Production: This process allows for a long production runtime of consistent shapes, which can be highly efficient.
- Variety of Materials: Different types of plastics can be extruded, enabling diverse applications within the Polaris 50 range.
- Cost-Effectiveness: Extrusion often requires less energy compared to other methods, which can translate into lower costs for the end product.
Nonetheless, one of the main challenges of extrusion is the potential for defects. Variations in thickness or density can occur if the extrusion parameters are not meticulously controlled. Such issues can impact both the appearance and durability of the final products.
Blow Molding
Blow molding is a technique specifically crafted for producing hollow parts, playing a pivotal role in the manufacturing of containers or ducts that form part of the Polaris 50 architecture. The process involves creating a plastic parison that is inflated into a mold using air pressure. Its key characteristics include:
- Hollow Structures: Ideal for creating lightweight, hollow designs that can be complex in shape.
- Fast Cycle Times: The blow molding operation can be quick, which speeds up production.
- Material Optimization: It also allows for the use of recycled plastics, addressing sustainability considerations in production.
However, blow molding does have drawbacks. The design flexibility is somewhat constrained compared to injection molding, particularly when it comes to more complex shapes. Additionally, the process can require substantial capital investment, particularly for molds and machinery.
"The choice of manufacturing process not only affects the efficiency of production but can also shape the functionalities and lifespan of the final product."
Properties of Polaris Plastics
Understanding the properties of Polaris 50 plastics is vital for anyone involved in the automotive industry. The plastics selected for making components in these vehicles are not arbitrary choices; they are informed by a thorough understanding of how they will perform under various conditions. Key factors such as durability, resistance to environmental factors, and weight play significant roles in the overall performance of the vehicles these plastics comprise.
Durability
Durability is one of the primary strengths of Polaris 50 plastics. This attribute ensures that components withstand the rigors of daily use, from the routine bumps and scrapes to the more severe impacts that can occur on the road. For instance, the use of polycarbonate in certain exterior parts provides a robust shield against cracks and breaks, making it a suitable choice for both safety and aesthetic elements. In practical terms, this means owners spend less time and money on repairs, contributing to overall vehicle longevity.
Moreover, the toughness of these materials allows the vehicles to maintain their structural integrity even under significant stress. This is crucial for performance, as any compromise in component durability can lead to a cascade of failures elsewhere in the vehicle. Essentially, selecting durable plastics fosters confidence in the vehicle's reliability and reduces the likelihood of unexpected breakdowns.
Resistance to Environmental Factors
The ability of Polaris 50 plastics to resist environmental factors is another layer to their utility. Simply put, these plastics are designed to handle exposure to elements like UV radiation, moisture, and extreme temperatures. For example, a plastic part that is not UV-resistant can deteriorate rapidly when exposed to sunlight over time. The included stabilizers and additives in the formulation of these plastics ensure that they resist fading and structural degradation longer than standard options.
On top of that, resistance to chemicals is vital, especially in components that might come into contact with oils, fuels, or cleaners. Materials like polyethylene and polypropylene shine in this aspect, as they provide excellent barrier properties against various substances, which is a necessity for maintaining the integrity of automotive components. In short, choosing materials that can withstand the elements prolongs the life of the vehicle and enhances consumer satisfaction.
Weight and Impact on Performance
The weight of the plastic used in construction influences not just the performance of the vehicle, but also fuel efficiency. Lightweight plastics such as ABS or polypropylene help in reducing the overall mass, which allows for better gas mileage—a factor increasingly important for modern consumers. A lighter vehicle is easier to accelerate, which can translate to a more responsive drive.
Moreover, weight considerations play a role in safety as well. There's a careful balancing act between achieving lightweight construction and maintaining high safety standards. Numerous studies indicate that reducing weight through advanced plastic materials does not compromise crashworthiness, but rather contributes to more effective energy absorption during an impact.
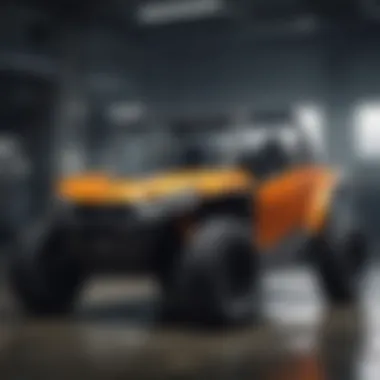
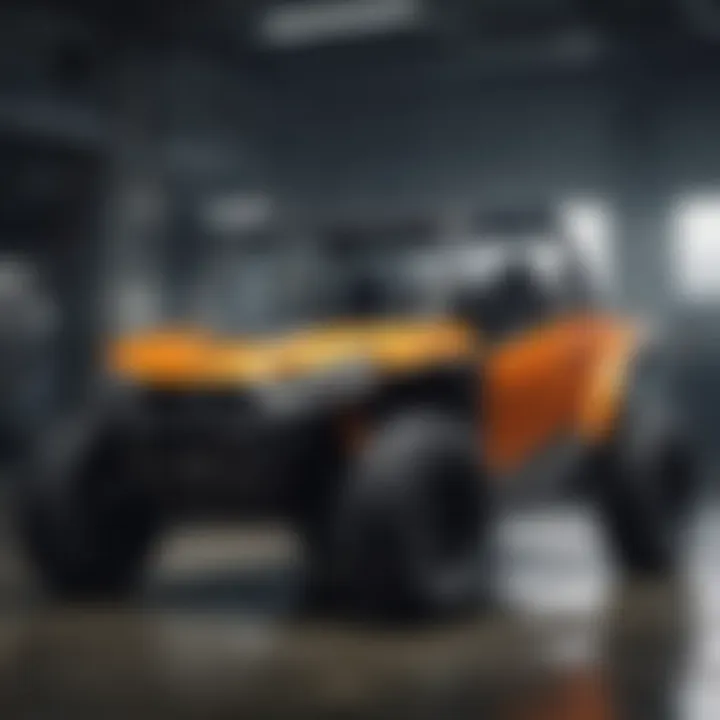
"Lightweight plastics in automotive design are not just about saving weight, but also about enhancing performance and safety."
In summary, the properties of Polaris 50 plastics encompass far more than their physical appearance. These materials are engineered with a keen awareness of performance metrics and environmental interactions, leading to improved durability, excellent resistance to adverse conditions, and a favorable impact on both weight and performance. The integration of these attributes into the Polaris 50 model system exemplifies a forward-thinking approach in the automotive industry.
Applications of Polaris Plastics in Automotive
The use of Polaris 50 plastics is pivotal in the automotive industry, shaping the durability, functionality, and aesthetics of vehicles. Various elements make these plastics indispensable, particularly their lightweight nature, resistance to environmental factors, and ability to be molded into intricate shapes. This section delves into the applications of these plastics, presenting a thorough exploration of how they contribute to different components of vehicles.
Exterior Components
When it comes to the exterior of a vehicle, Polaris 50 plastics play a vital role. They are often used in the production of body panels and fascias due to their high impact resistance and ability to withstand various weather conditions. Unlike traditional materials, these plastics don’t easily rust or corrode, offering a longer lifespan for exterior elements.
Moreover, the lightweight nature of these plastics contributes to improved fuel efficiency. By reducing the overall weight of a vehicle, manufacturers can enhance performance without having to compromise on strength. Some key advantages of using Polaris 50 plastics for exterior components include:
- Durability: Capable of enduring harsh conditions, from intense sunlight to freezing temperatures.
- Customization: Flexible enough to be molded into complex shapes, giving manufacturers creative freedom.
- Cost-Effectiveness: Generally more affordable than metal options, reducing manufacturing costs.
"The shift towards using plastics in car exteriors highlights the automotive industry’s commitment to innovation and sustainability in design."
Interior Components
In contrast to the tough exterior, the interior of a vehicle encapsulates comfort and user experience. Polaris 50 plastics contribute significantly by being used in dash panels, door trims, and seating components. Their lightweight nature means more room for features and electronics, and they can be designed to absorb sound, which enhances ride comfort.
The materials are also easy to clean and maintain, making them practical choices for daily use. When it comes to aesthetics, Polaris 50 plastics can be manufactured in a multitude of finishes and colors, allowing manufacturers to deliver a variety of automotive themes. Key features include:
- Aesthetics: Ability to imitate wood, metal, or any finish desired, offering a luxury feel.
- Comfort: Soft touch plastics reduce harshness, providing a relaxed driving environment.
- Functionality: Many interior plastics are designed with features like integrated storage or cup holders.
Functional Parts and Accessories
Beyond the basic interior and exterior components, functional parts and accessories also benefit from the versatility of Polaris 50 plastics. This includes items like brackets, housing for lights, or other fittings essential for a vehicle's operation. Using plastic in these applications can lead to a significant reduction in weight, which is crucial for enhancing the overall efficiency of the vehicle.
A few considerations when using these plastics in functional parts are:
- Precision: Plastics can be molded precisely, allowing for a better fit of each component, which can lead to longer-lasting assemblies.
- Safety Features: Many modern safety elements, like airbags and their housing, utilize advanced plastics, ensuring they meet stringent safety standards.
- Electrical Insulation: These plastics provide excellent insulation properties, reducing risks and enhancing safety in electronic applications.
In summary, the applications of Polaris 50 plastics step beyond mere utility; they are integral to crafting vehicles that are aesthetically pleasing, functional, and durable. The ongoing innovations in this realm are turning heads within the automotive industry and beyond.
Environmental Considerations
Environmental considerations are increasingly prominent in discussions surrounding automotive design and manufacturing. In the case of Polaris 50 plastics, these considerations become crucial, touching upon both sustainability and end-of-life recycling processes. Recognizing the environmental impact of the materials used not only helps manufacturers keep in line with regulations but also aligns with the growing consumer demand for eco-friendly practices. This section delves into the key aspects of sustainability and recycling associated with Polaris 50 plastics.
Impact on Sustainability
Sustainability in the automotive industry is no longer just a buzzword—it's a necessity that plays a central role in product development. With rising concerns over climate change and resource depletion, manufacturers of Polaris 50 components are under pressure to adopt materials and processes that minimize environmental harm.
The plastics used in the Polaris 50 line often boast a range of sustainable features:
- Reusability: Many of these plastics can be reused in various applications, reducing the need for new materials.
- Lightweight Construction: Utilizing lighter materials decreases fuel consumption of vehicles, which leads to lower emissions. This characteristic is particularly significant given the automotive industry's push towards more fuel-efficient designs.
- Sourcing Practices: By selecting recyclable or sustainably sourced plastics, manufacturers can lessen their environmental footprint and demonstrate corporate responsibility.
Moreover, the production process for these plastics can be refined to reduce energy consumption and waste. Companies investing in greener technologies often see a positive return on investment while improving their public image and customer loyalty.
"Sustainable practices in automotive plastics matter not just for the planet, but also for a brand's resonance with customers."
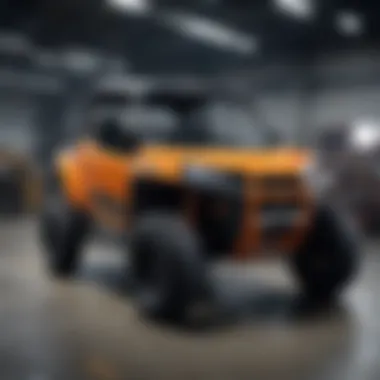
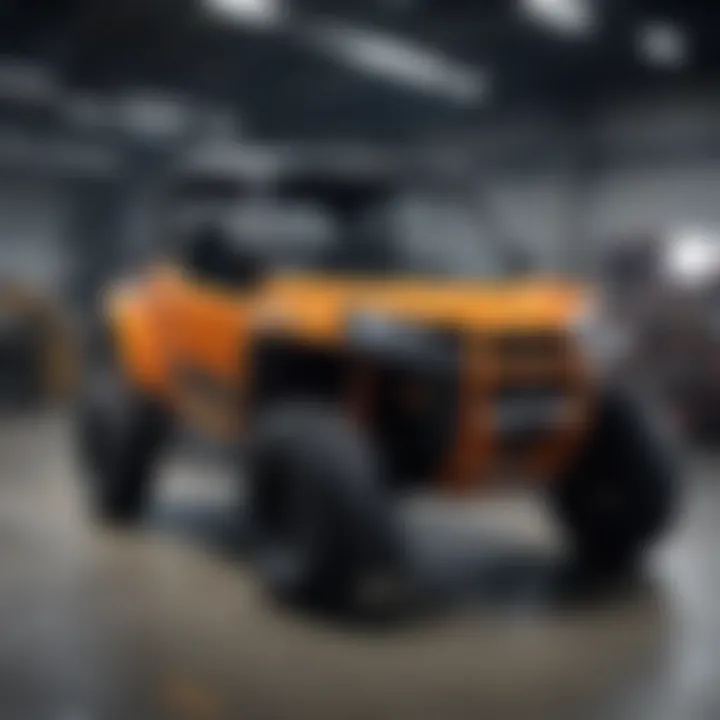
Recycling Processes for Automotive Plastics
Recycling processes for automotive plastics are another vital component of environmental considerations. The essence here is not just to utilize plastics effectively but to ensure they don't end up polluting landfills once their lifecycle as a product is complete. The Polaris 50 vehicles create a robust framework for integrating recycling into their life cycle.
Key methods in the recycling of these plastics include:
- Mechanical Recycling: This is the most common method where plastics are shredded, melted, and reformed into new products. It's a straightforward process that often yields quality materials for reuse.
- Chemical Recycling: Unlike mechanical recycling, this method breaks plastics down to their original monomers, allowing for a more versatile repurposing. It can revitalize materials that may not be suitable for mechanical processes due to contamination or degradation.
- Energy Recovery: For plastics that are difficult to recycle, energy recovery methods can be applied. By incinerating non-recyclable plastics, energy can be generated, offsetting some of the fossil fuels needed in production.
In summary, effective recycling processes mitigate the environmental impact of production and consumption while reinforcing sustainability efforts. Companies that focus on innovation in their recycling methods can lead the way to a more circular economy in the automotive sector, ensuring that Polaris 50 plastics contribute positively to the environment even after their service as vehicle components.
These environmental considerations not only enhance the operational efficiency of manufacturing but also resonate with a customer base that increasingly values sustainability in their vehicle purchases. As this trend continues, companies that prioritize these aspects are likely to find their products more appealing to a modern audience.
Future of Plastics in the Automotive Sector
The automotive industry is constantly evolving, and understanding the future of plastics within this sector is a key component of that evolution. As vehicles become more complex and technology advances, the role that plastics play cannot be overstated. The shift towards lightweight materials, improved safety features, and enhanced aesthetic appeal are driving changes in how manufacturers approach automotive design. Moreover, environmental concerns are also shaping the direction of plastic use, making this topic increasingly relevant.
To break it down, a few specific elements have emerged that signify the importance of plastics in future automotive applications:
- Weight Reduction: Given the ongoing push for fuel efficiency and reduced emissions, lightweight plastics help manufacturers meet stringent regulations while enhancing vehicle performance.
- Safety Enhancements: Advanced polymers are increasingly used in impact-resistant components, providing better passenger protection without adding significant weight.
- Cost-Effectiveness: With the ability to mold complex shapes and reduce assembly time, plastics offer a more economical option compared to traditional materials like metal.
As we look toward the future, technological advancements and shifts in consumer preferences play significant roles in defining the trajectory of plastic use in the automotive landscape.
Technological Advancements
Recent innovations in material science have sparked a flurry of developments within the plastic domain. New formulations and manufacturing methods are emerging, changing the game for plastics in vehicles. For instance,
- Smart Plastics: These materials incorporate sensors and responsive features that can communicate with automotive systems, enhancing safety and functionality.
- Biodegradable Options: There is growing research into compostable plastics, which could drastically reduce the environmental footprint associated with automotive waste.
- 3D Printing: The arrival of additive manufacturing allows for on-demand production of complex plastic components, reducing waste and inventory costs. This technology has the potential to revolutionize how parts are manufactured and supplied in the automotive sector.
As these advancements converge, they present exciting opportunities for automakers to innovate while creating vehicles that are lighter and more efficient.
Trends in Consumer Preferences
Consumer preferences are crucial for shaping the trajectory of plastics in the automotive industry. Today's buyers are more conscious about not just performance but also the environmental impact of their vehicles. Some notable trends in this domain include:
- Sustainability Concerns: An increasing number of consumers opt for products made from recycled materials. Automakers that incorporate sustainable practices in their plastics' production appeal to buyers who prioritize environmental stewardship.
- Customization: There is a surge in demand for personalized and unique designs. Plastics offer versatile characteristics that allow for a degree of customization in both the interior and exterior of vehicles.
- Safety and Comfort: Buyers today are seeking vehicles that not only have aesthetic appeal but also emphasize safety features. Advanced plastic materials can provide the durability and flexibility needed to meet these demands.
Looking ahead, understanding how consumer preferences evolve will be essential for automakers who aim to stay ahead of the curve and align their products with what buyers want. The interplay of new technological advancements and changing consumer attitudes heralds a promising future for plastics in the automotive sector.
"The future is not something we enter. The future is something we create." - Leonard I. Sweet
As we continue down this path, it is essential for industry players to remain adaptable and responsive to both technological opportunities and consumer sentiments in order to fully leverage the advantages that plastics offer.
Closure
In wrapping up our exploration of Polaris 50 plastics, we find a wealth of insight surrounding its potent relevance in the automotive industry. The significance of understanding this topic cannot be understated, especially when considering the structural and functional benefits these materials bring to vehicle design and performance. This examination has woven together the journey from plastic types through manufacturing processes to environmental implications, presenting a detailed tapestry of knowledge that automotive enthusiasts and industry professionals alike will find invaluable.
Recap of Key Insights
- Diverse Material Types: The Polaris 50 employs various plastics, such as polypropylene and ABS, each with unique properties tailored for specific applications. These selections underpin much of the vehicle's performance and durability.
- Manufacturing Techniques: Different methods like injection molding and extrusion are integral to the shaping of plastics, ensuring parts are both lightweight and resilient, crucial traits for modern vehicles navigating diverse conditions.
- Environmental Perspectives: The article has highlighted pressing concerns related to sustainability. As the push for recycling and eco-friendly materials gains momentum, it is essential to explore how Polaris 50 can adapt and lead in this arena.
- Future Outlook: Innovations in technology promise to further enhance the functionality of plastics in automotive use, aligning them with evolving consumer expectations and environmental standards.
Final Thoughts on Polaris Plastics
As we conclude, it becomes evident that the exploration of Polaris 50 plastics is not just an academic exercise but a vital inquiry into the future of automotive design. Recognizing the performance capabilities and sustainability considerations leads to more informed decisions for manufacturers and consumers. In a time when eco-consciousness and technological advancement are at the forefront of industry trends, Polaris 50 exemplifies how plastics can still play a pivotal role. Embracing these insights equips stakeholders with the knowledge to drive change, fostering innovation that respects both the consumer base and the environment.
Looking forward, it is clear that Polaris will continue to thrive by adapting its plastic applications to not only meet today’s challenges but also anticipate those of tomorrow. As interest in greener solutions increases, the discourse surrounding plastics in the automotive sector, particularly with regards to Polaris 50, only promises to deepen.
"The road ahead is paved not just with technology, but with an understanding of how our choices shape the future. "